Omegasonics In 4 Steps
1. Transducer Construction
The transducer is the same as a stereo speaker, just ours is placed in a liquid bath. We vibrate the woofer cones at a high frequency to create mechanical, high pressure vacuum bubbles that implode and rip the dirt off your part.
What makes our transducers special?
Our piezo-electric crystals are cured for a minimum of three months in a climate and humidity controlled room. Pzt’s are then sorted and grouped to operate within a 2% capacitance range so that the transducers we build for you today will be the same as the transducers we build for you in the future. Couple this scrutiny with an exacting detail for bolt torquing of the pzt stacks, creates an unparalleled level of longevity.This intense level of exactness provides our customers the most consistent performance in our industry.
2. Generator Construction
The ultrasonic generator serves the same purpose as your stereo receiver. It sends a very specific electrical frequency signal to the transducer to produce the exact cleaning frequency for your application. Unlike a typical car stereo, the ultrasonic generator sends a base frequency which also sweeps over of a small bandwidth to create chaos in the cleaning bath – eliminating standing waves and bottom line, does a better job of cleaning your parts.
What makes our generators special?
Omegasonics generators are manufactured entirely in the United States under very controlled conditions. Each power board is individually soldered to insure exacting solder fill joints. Control boards are also manufactured in the United States by high precision SMD robots utilizing a digital microprocessor for controlled sweep frequencies. Each finished assembly is tested under full load for a minimum of one hour to ideliver solid, uninterrupted performance in the field.
3. Machine Assembly
Silicone heating elements are glued to the outside tank surfaces and the tank is then insulated with foil faced fiberglass. Tank is dropped into the portable frame housing and the completed transducers are then bolted into the bottom of the tank. The electrical back and front panels are installed as well as level sensors, plumbing pump and filters. The ultrasonic generator is then connected, the tank is filled with water and tested for eighteen hours to insure proper operation with no leaks.
What makes our machine assembly special?
Each machine is individually handcrafted to provide years of easy operation and reliable service. Throughout each phase of construction, a QC manager certifies that all construction steps have been properly met based on our detailed construction guidelines.
4. Shipping
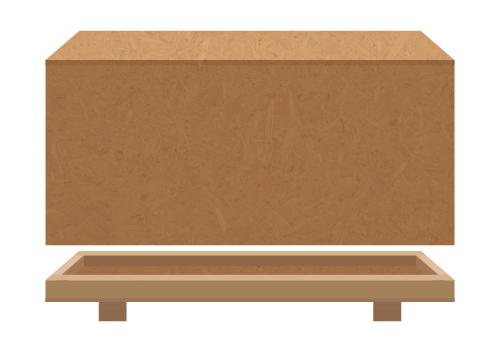
Once the ultrasonic washer is tested, QC’d and documented, it is drained, wiped dry, all panels securely fastened and the machine is wheeled into the shipping department. The unit is paper pad wrapped, shrunk wrap and placed on a solid pallet base, secured to the base, and a complete crate is built around the machine to protect it for freight transport.
What makes our shipping process special?
We take every necessary precaution to secure internal components, especially the ultrasonic generators and build a custom crate assembly for each of our units. The bases the equipment rest on are solid and the machines are placed on 2×4 riser so the wheels do not take any impact from dropping in transit. Units are strapped in multiple locations to the pallet to restrict motion in transit. The crating construction is so robust, we get comments from clients that are shipping crates are built better than some houses.