Aerospace and Defense Clients are Taking Ultrasonic Cleaner Technology to New Heights
Aerospace and defense clients are involved in designing, building and maintaining man made aircraft for travel through earth’s atmosphere as well as spacecraft for flight into outer space. Our ultrasonic cleaners play a significant role in supporting this mission.
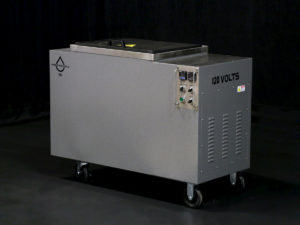
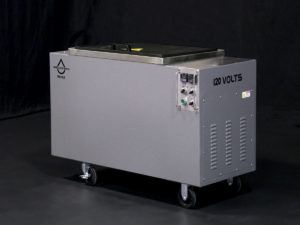
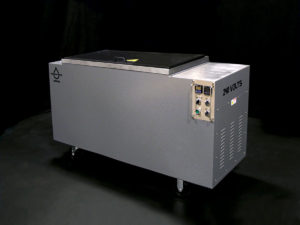
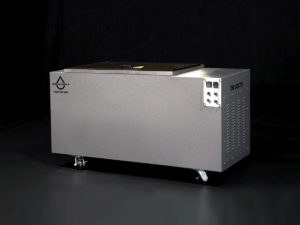
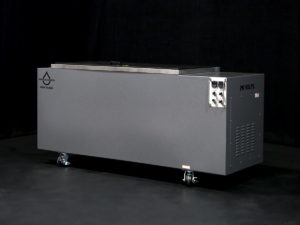
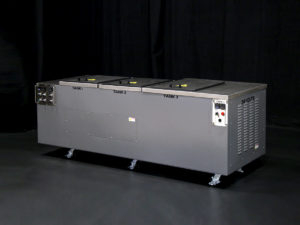
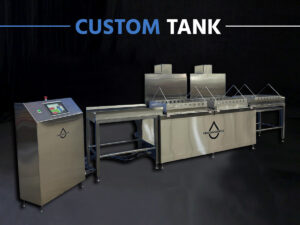
Eaton Saved More than 20 labor hours and minimized Employee Chemical Exposure.
Eaton Aerospace in Jackson, Michigan, has been making critical parts for sophisticated aircraft since 1940. They bend stainless steel tubing into complex shapes for the world’s largest passenger planes and the country’s newest fighter jets – a complicated process requiring meticulous cleaning and the highest quality standards at every stage. Hand-scrubbing with chemical solvents used to require a minimum of 20 hours of labor each week and additional runoff management costs. After getting to know Omegasonics at a trade show, Eaton asked us to customize and retrofit their “hands-off” ultrasonic units to clean their uniquely shaped and sized hydraulic tubes. Eaton saved more than 20 labor hours and minimized employee chemical exposure.
Omegasonics wasn’t the cheapest or the most expensive. They had an excellent product for the money and a commitment to customer service. Omegasonics is very easy to work with, even from 2,000 miles away. The retrofit and all other support needs have been handled in a very responsive manner. Omegasonics’ dependability and service are part of our operational success. As far as our employees and management are concerned, our Omegasonics units are here to stay. For any future needs, Omegasonics is our #1 choice.
– Bud Greener, Manufacturing Engineer, Eaton Aerospace
Get exactly what you need.
We have more than 50 existing ultrasonic units to choose from. Units can be customized and retrofit by the Omegasonics team, like the units Eaton Aerospace uses, but an existing model may do just fine. Every unit offers our clients the same benefits.
- High-quality, precision results with even intricate pieces or uniquely shaped or sized parts
- Lower labor costs and increased production efficiency
- Easy to use and setup; no training required
- Reduces the use of toxic solvents and expensive waste removal services
- Uses only EPA-approved water-based solutions
Case Study
Learn why Eaton Aerospace decided to pursue an environmentally friendly solution to their cleaning needs. This after years of cleaning tubing with mineral spirits and Stoddard solvent.